Summary
- Secure materials properly to avoid skewed engravings
- Test speed & power settings on scrap material before finalizing
- Always double-check focus and ensure proper ventilation to keep laser engraving clean and sharp.
When I started laser engraving, I expected a learning curve — but not the kind that would waste entire afternoons. Many of the mistakes I made seemed small at the time, but they ruined projects or forced me to start from scratch. These five missteps were the most frustrating because they were avoidable once I knew what to look for. Learning from my experience could save you a lot of time and headaches if you’re diving into laser engraving.
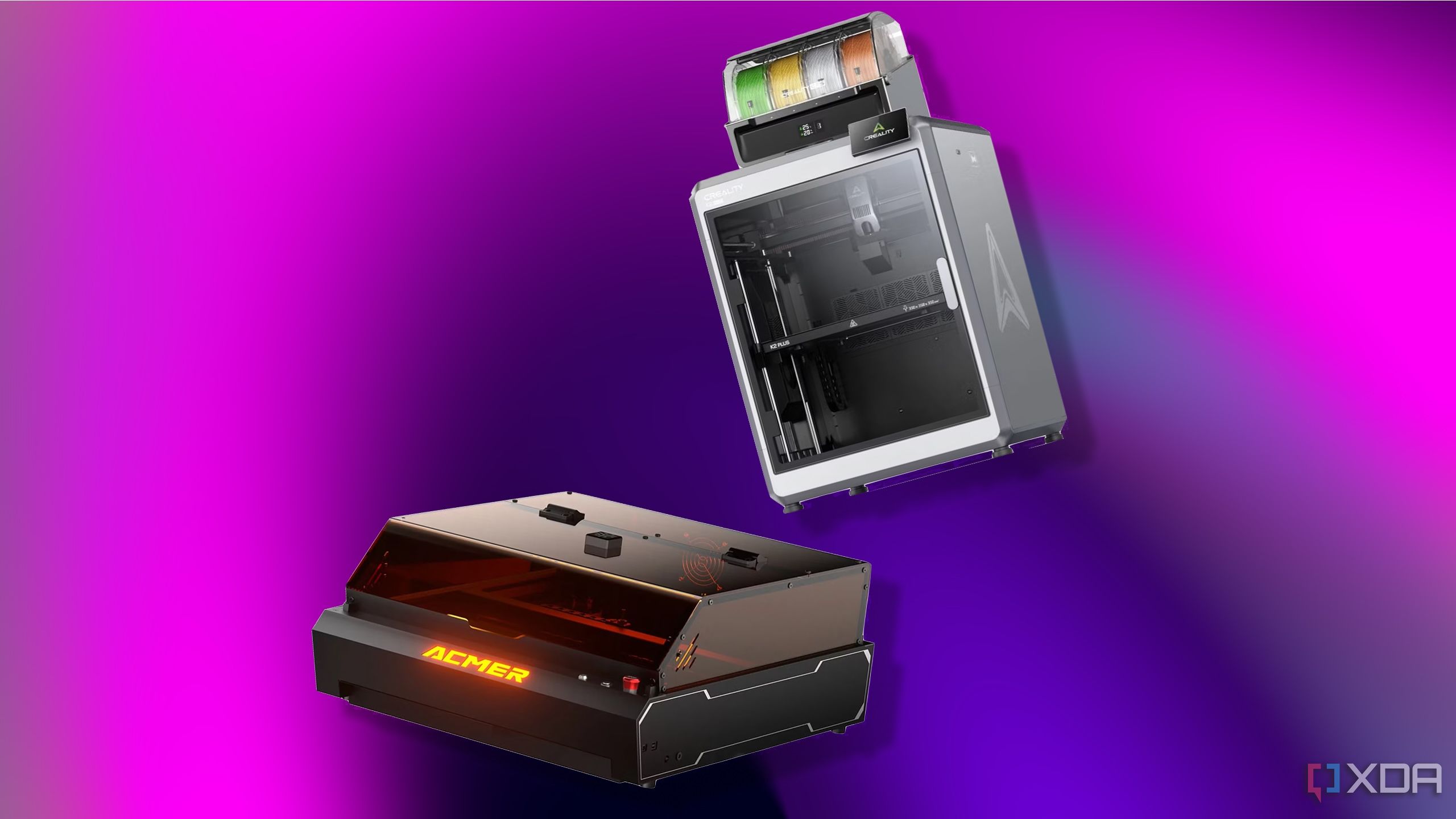
Related
I discovered 5 projects that blend 3D printing and laser engraving
I don’t think my love of laser engraving or 3D printing is a secret, but even better would be combining the two. These projects do just that
5
Not securing the material properly
Unclamped or crooked materials ruin engravings fast
One of my earliest mistakes was placing material on the bed and trusting gravity to keep it in place. That might work if you’re engraving something super light, but anything larger or slightly warped can shift mid-job. I had several engravings go off-center or skewed because the board moved just enough to ruin alignment. It was frustrating to see good designs botched by something so basic.
Once I realized the issue, I started experimenting with ways to hold things down. Magnets are ideal for metal honeycomb beds, while silicone bumpers, tape, or edge clamps are more suitable for wood or acrylic. I also double-check squareness with a corner jig or manually lining up the laser head. Even just a little preparation here makes a huge difference.
Flatness matters just as much as security. A bowed board can throw off the laser focus, especially on detailed raster engravings. Now I check each material for warps and flip or shim it if needed. It’s a simple routine, but it saves me hours of frustration and wasted materials.
4
Using the wrong speed and power settings
Generic settings don’t work for every material
Laser software often includes presets, but they’re not always reliable. I tried running default settings on a bamboo board once, and it left barely any mark. Then I slowed the speed, doubled the power, and scorched the whole piece. Every material has its quirks, and what works for one type of wood might ruin another.
I learned to start small: run test burns in a corner or on a scrap piece of the same material. I make a quick grid of different speed and power combos, label them with a marker, and pick the best result. That one step helps me dial in the ideal settings before committing to the final design, saving me time and materials.
Keeping track of those results is key. I started a spreadsheet with each material I used, its thickness, and the best settings. Over time, that database became a huge time-saver. Now I can go back to my previous jobs and reproduce results instead of starting from scratch every time.
3
Forgetting to focus the laser
A tiny focus error ruins sharpness and depth
This is one of those mistakes you might not notice until you’ve already ruined the job. I once engraved a slate tile that came out slightly fuzzy, and I couldn’t figure out why until I realized the material was thicker than usual and hadn’t adjusted the focus. Even a few millimeters off can make your engravings look soft or uneven.
I now use a metal spacer or the focus stick that came with the machine. After placing the material, I lower the laser module to the correct height and double-check by running a short line. If you’re doing repeat jobs on the same material, you can save those measurements for next time.
If your machine has autofocus, don’t assume it’s infallible. I’ve seen autofocus fail when the material wasn’t flat or had a reflective surface. It’s worth doing a visual check, especially for thicker or irregular pieces. A properly focused laser always gives cleaner, more consistent results, and you only need to be off once to start making it a habit.
2
Ignoring airflow and ventilation
Smoke buildup messes with the laser beam
In the beginning, I thought the built-in exhaust fan would be plenty. But the first time I engraved acrylic for 30 minutes straight, the whole workshop smelled like melted plastic, and the result was a mess. Smoke particles hung in the air, scattering the laser beam and dulling the engraving. It didn’t take long to realize that poor ventilation doesn’t just stink — it also hurts output quality.
I eventually added a 4-inch inline fan that vents outdoors, and the difference was immediate. I also turn on the built-in air assist to blow directly at the engraving point. That small stream of air helps clear smoke as it forms, keeping the laser path clean. Both upgrades make my engravings sharper and more detailed, even on smoky materials like leather or MDF.
Indoor setups need extra attention. Since I only engrave indoors, I run an air purifier connected directly to the exhaust fan of my laser engraver. It doesn’t take much smoke buildup for results to go downhill fast. Clean airflow helps the machine run longer and makes the space safer for you to work in. If your engraver is near a window, opening it will also help tremendously. It’s one of the easiest and most impactful things to upgrade.
1
Starting jobs without double-checking the design
Tiny mistakes in the file cause a big waste of time
Design mistakes are the worst because you don’t notice them until the job’s almost done. I’ve flipped images incorrectly, left layers hidden, or forgotten to convert text to outlines. Every one of those mistakes has cost me at least one ruined piece and a big chunk of time. Once, I engraved a mirrored design onto glass — except I forgot to actually mirror it.
Now I preview everything, even if I’m 99% sure it’s right. If the software supports camera preview, I’ll use it to align the job precisely. Otherwise, I run a frame trace or use a light pointer to confirm placement — a few extra seconds of checking beats redoing an entire project.
Design software can also trip you up. Vector lines might be set to “hairline” but not assigned as a cut in the laser program. Text might default to raster instead of vector. That’s why I inspect every object, check the order of operations, and save a backup before sending it to the machine. Getting into that habit has spared me from more do-overs than I can count.
Small habits can prevent huge time losses
Every mistake came from moving too fast or skipping a step, I thought didn’t matter. However, in laser engraving, minor errors turn into big problems. You can avoid hours of rework by slowing down just a little—securing the material, testing settings, double-checking focus, ensuring airflow, and reviewing your design. These habits didn’t just improve my results; they made the whole process more fun and less frustrating.