Summary
- Combining laser engraving with 3D printing creates unique, customizable items quickly and inexpensively.
- Creative projects like edge-lit lamps, kinetic coasters, and wood-inlay magnets showcase the enhanced capabilities of blended fabrication techniques.
- Building a DIY laser engraver from 3D-printed parts offers cost-effective customization and a deeper understanding of the technology.
Integrating a laser engraver with a 3D printer opens a playful middle ground between two very different fabrication styles: one lets you build in three dimensions, the other carves beautiful two‑dimensional detail. There are a few projects I definitely want to try for myself, showing how combining the two machines creates objects that feel richer and far more personal than either tool can manage alone.
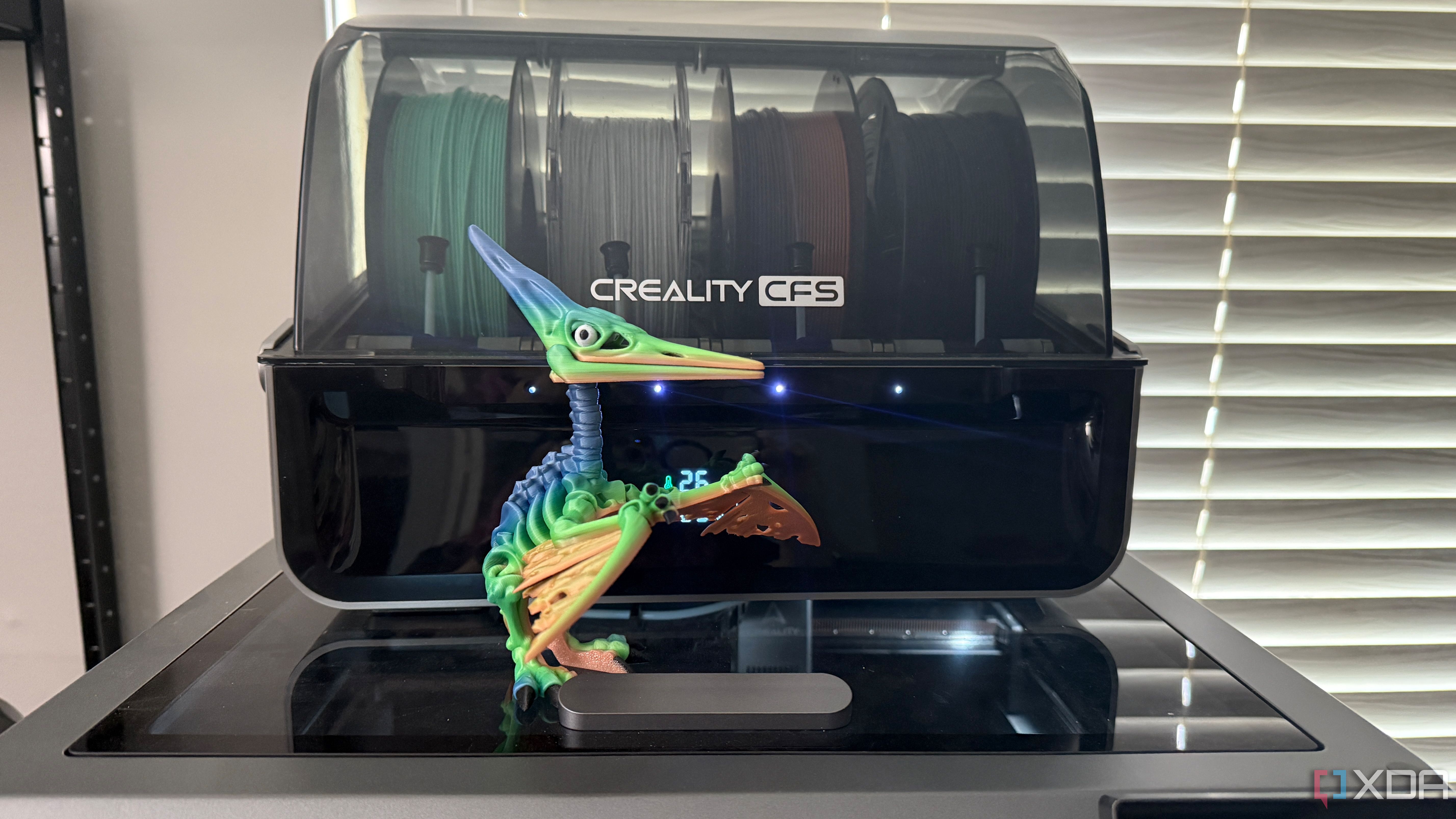
Related
Sometimes I run out of ideas; here are 7 ways I find new 3D printing projects
We all hit creative blocks sometimes, but there are plenty of places to look for inspiration for your next 3D printing project
5
Edge‑lit acrylic desk lamp build
Why lighting up plastic feels strangely satisfying
The classic edge‑lit sign gets a maker’s upgrade by slipping a laser‑engraved acrylic panel into a snug, 3D‑printed LED base. The base prints in one piece, tapering toward a narrow slot that captures the panel and hides a short LED strip wired to a tiny rocker switch and a 12V wall brick. Because the panel’s artwork is engraved, not surface‑printed, it glows evenly along every scored line when the LEDs power on, creating an illusion of floating light shapes.
Design work happens in two stages: vector art for the laser and CAD for the base. Most makers sketch the panel in Inkscape or Illustrator, export an SVG, then run a shallow engrave pass on 3mm clear acrylic. Meanwhile, the base can be modeled in Tinkercad or Fusion 360 with a simple electronics cavity and press‑fit diffuser window. The two parts meet with near-zero finishing — simply peel the acrylic’s masking film, slip everything together, and secure the LED strip with hot glue or double-sided tape.
What makes this hybrid lamp shine (pun unavoidable) is customization speed. Swapping a different panel takes minutes and costs pennies, so seasonal artwork, game logos, or even a quick night‑light silhouette all fit the same printed base. The job rarely tops a four‑hour print and a five‑minute engrave, yet the finished piece looks upscale enough to gift or sell at craft fairs without feeling mass‑produced.
4
Self‑moving kinetic drink coaster set
Because your beer deserves gentle orbital motion
Designer DIY Machines created a coaster system that quietly spins your glass while friends try to figure out how it works. The trick involves a coin-cell-powered DC motor and Hall sensor hidden inside a 3D-printed base. Once a coaster with an embedded magnet lands on the base, the motor engages and starts the slow rotation. The tops can be either laser‑cut hardwood or engraved acrylic, giving you intricate surface graphics to match the hypnotic movement.
Files are supplied for both fabrication paths, but running them together gives the best of each: print the hinged housing, then engrave geometric or fandom artwork onto thin plywood discs. Assembly stays tool‑light—press‑fit bearings, a dab of CA glue, and two solder joints. The maker notes that switching to rechargeable Li-ion coin cells extends runtime without redesigning the case, allowing you to keep the party spinning all evening.
Beyond novelty value, the project acts as a showcase for machine tolerances. The printed shell needs tight alignment so the platter clears the lip by less than half a millimeter, while the laser affords letter‑perfect artwork at 0.1 mm line width. It’s an addictive demonstration piece that inevitably nudges visitors to ask how they can build one.
3
Snapmaker coaster engraving alignment jig
Quick swaps keep your coffee rings precise
If you own a Snapmaker or any small diode engraver, you know repeatability can be frustrating when personalizing dozens of slate or ceramic coasters. A simple 3D‑printed jig solves that as it frames a 100mm tile with corner stops, sits flush against the machine’s origin, and guarantees every coaster lands under the laser in precisely the same spot.
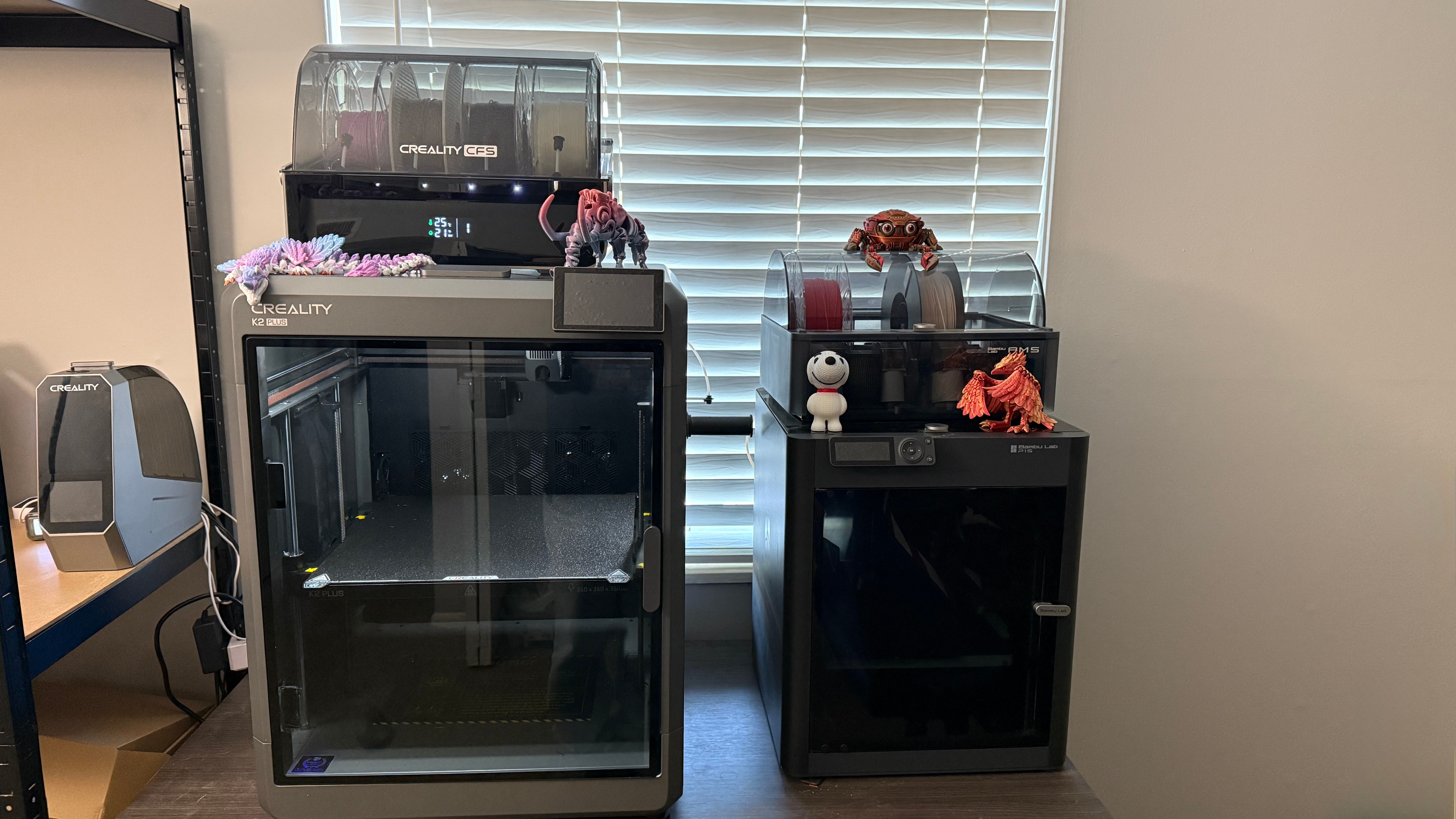
Related
I try to convince everyone to get into 3D printing, and these are the 4 reasons I think you should
After 3D printing for several years, I recommend that anyone buy a 3D printer for the following four main reasons.
Printing takes about an hour and uses barely 20g of PLA, yet the payoff is enormous when you batch‑run gifts or Etsy orders. Once the jig is on the bed, you knock out one test engrave to dial in focus, then drop‑swap tiles without changing the job’s coordinates. Makers report throughput rising from four coasters an hour to a steady ten because the design eliminates constant tape‑and‑measure shuffling or camera calibration. Print a matching stack rack for extra polish that cools finished tiles while you engrave the next set. Drop‑in parts like these turn two machines into a minimal production line: the printer fabricates fixtures; the laser handles artwork; your hands just load blanks and collect finished pieces.
2
Wood‑inlay 3D printed fridge magnet
State shapes with magnetically charged fridge personality
Several Glowforge owners have delightful mashups: combining PLA 3D prints with laser‑cut wood insert (or vice versa) that snap in flush, hiding a neodymium magnet tucked behind the inlay. The printed frame gives organic curves and a living‑hinge‑style lip, while the laser captures grain detail no FDM layer can touch.
The workflow is refreshingly short. Model the outline in CAD, export a matching SVG, and offset the vector by twice the laser’s kerf so the wood press‑fits the plastic. Cut the insert from 1.5 mm walnut veneer, finish it with a quick wipe of oil, then press it into the printed cavity while the PLA is still warm from the plate. A drop of CA glue at the rear edge keeps the magnet seated.
Because the idea scales to any silhouette — pets, logos, meme shapes — it’s a crowd‑pleasing stocking stuffer that teaches kerf compensation in a single afternoon. Mixing matte-printed plastic with warm wood grain elevates a humble fridge magnet into something that looks boutique‑store-ready.
1
Homebuilt 3D printed laser engraver
When buying one feels far too ordinary
Finally, if you would rather create the tool, check out the 38×29cm DIY engraver, whose chassis is almost entirely 3D‑printed. The builder designed motor plates, belt holders, and distance bushings in PLA and ABS, then bolted them onto inexpensive aluminum extrusion for a rigid frame that accepts a 2W laser diode. The result is a serviceable engraver for under $215 in parts and a weekend of printing.
Step‑by‑step instructions cover everything from tensioning GT2 belts to flashing GRBL on an Arduino Nano. Calibration jigs — also printed — help dial wheel spacing, so the carriage holds position even when the frame stands vertically, proving that printed mechanics can remain precise with the correct infill and bolt preload.
Why bother when you can buy a kit? First, you learn how an engraver ticks, making future upgrades less mysterious. Second, replacement parts cost pennies because you print them on demand. And third, ownership pride is real when friends realize the machine engraving their coasters sprang from your own slicer.
Mixing tools unlocks new creative superpowers for makers everywhere
Whether you edge‑light acrylic art, mesmerize guests with spinning coasters, batch‑engrave café‑grade drink mats, craft boutique fridge magnets, or build the engraver itself, pairing 3D printing with laser work turns each machine’s limits into the other’s strengths. Try one of these mashups, and you’ll find that the design possibilities multiply faster than the projects pile up on your workbench.