Summary
- Adaptive layer height saves time and filament by adjusting layer thickness based on model geometry.
- Dropping perimeter count to 2 reduces waste, print time, and nozzle artifacts without compromising strength.
- Choosing efficient infill patterns like gyroid and cubic lowers filament use while maintaining strength and print quality.
I didn’t realize how much filament I was wasting until I started making minor changes to my slicer settings. What began as a few tweaks to speed up prints quickly turned into a full-on overhaul of how I sliced nearly everything. These aren’t obscure experimental features or gimmicks — they’re practical, everyday settings that made my prints cleaner, faster, and more efficient. If you want to reduce waste without sacrificing quality, these settings truly made a difference.
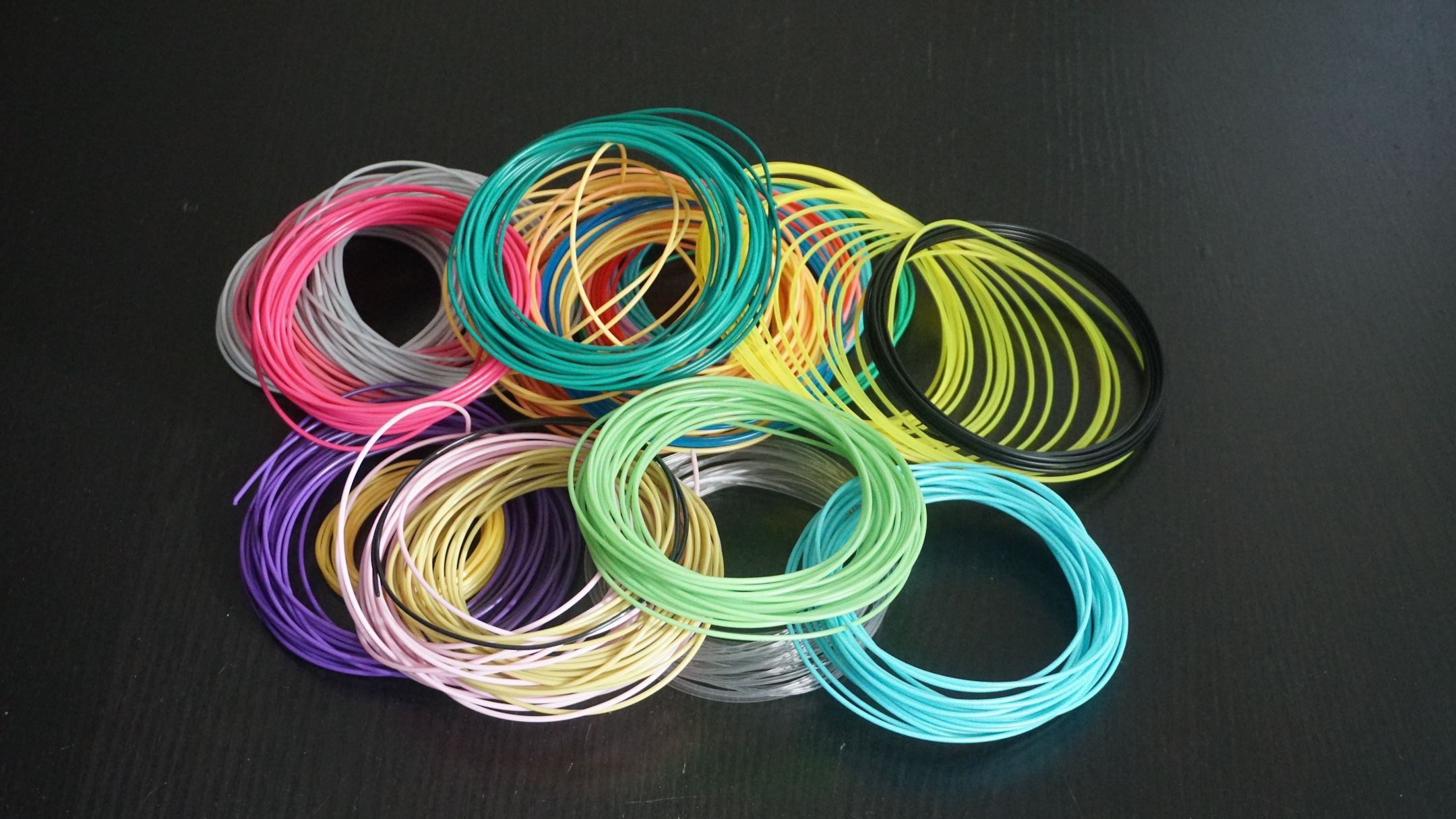
Related
4 ways to use recycled plastic as 3D printer filament
Reduce, reuse, recycle.
7
Switching to adaptive layer height
This setting cuts time and saves filament fast
Layer height significantly affects the length of a print and the amount of plastic it uses. Most slicers default to a fixed value like 0.2mm, which generally works well but doesn’t account for parts of a model that don’t need that level of detail. Adaptive layer height automatically adjusts the thickness of each layer based on the model’s geometry. Areas with fine detail get thinner layers, while flatter areas use thicker ones.
This approach speeds things up significantly while reducing filament use. You end up with fewer total layers, which means less material extruded overall. I’ve used it on everything from busts to brackets, and the results consistently look better than prints with fixed heights. It’s also an easy setting to enable — usually just a checkbox — so it’s one of the fastest wins you can get in any slicer.
You might need to adjust the minimum and maximum layer height values to suit your printer’s capabilities. I’ve found that 0.12mm to 0.24mm works great for most standard nozzle sizes. Once I made the switch, it became my default for almost every model I slice.
6
Dropping the number of perimeters
Fewer walls without compromising on strength
The number of perimeters — also called shells or walls — controls how many outlines the printer draws around each layer. While three is a standard default, I’ve found that dropping to two saves a noticeable amount of filament throughout a print. This is especially true for larger models, where walls account for a larger volume. Two walls have been perfectly fine unless the part needs extra strength or abrasion resistance.
Reducing wall count isn’t just about saving plastic; it also reduces print time. Less back-and-forth motion means faster layers and fewer chances for nozzle artifacts. For parts that need strength in specific directions, increasing infill or adding supports in key areas has worked better for me than adding more perimeters. It’s a more targeted way to strengthen prints.
Of course, there are exceptions. I still use three or even four perimeters for structural parts or those that will see high stress. But for decorative models or housings, two get the job done. Try a test print with a lower wall count — you might be surprised at how little difference it makes in appearance or durability.
5
Choosing more efficient infill patterns
Strength without wasting material on overkill grids
Infill is often one of the most significant sources of wasted filament. I used to rely on the default grid pattern, thinking it was a safe bet for strength. But after testing alternatives, gyroid and cubic infill types became my go-to choices. They provide more uniform strength in all directions and use less material. Gyroid, in particular, prints quickly and looks great in cross-section, too.
Another trick that helped was dialing down the infill percentage. Even going from 20% to 15% makes a big difference, especially on large prints. Decorative parts can often be printed with as little as 5% infill, as long as the outer walls are thick enough. For functional parts, I still keep it higher, but the switch in pattern alone helped reduce material waste without affecting performance.
One bonus I didn’t expect was how quiet some patterns are while printing. Less travel means less vibration and smoother movement, which is easier on the printer. It’s a win across the board, and once I saw the time and filament savings add up, I never went back to the grid.
4
Tuning support generation smarter
Fewer supports, better results, and easier cleanup
Supports are one of the biggest culprits when it comes to wasted filament. Most slicers overdo it by default, especially with conservative overhang thresholds set to 45°. Depending on the filament and part orientation, I started bumping mine up to 50° or even 55°. This small change sometimes cuts support usage by as much as 40%. The results were still clean, and cleanup was way easier.
Related
5 filaments that are better than PLA for serious 3D printing projects
While PLA definitely fills the 3D printing needs for many projects, other filament materials are better for more serious projects
Switching to tree supports in Cura also made a huge difference. They’re designed to grow toward the overhangs rather than fill the area below, dramatically reducing material use. They also break off more cleanly than traditional blocky supports, which means less post-processing and less chance of damaging a part. Tree supports feel like a cheat code for models with many overhangs. If you’re using a slicer that doesn’t offer tree supports, try enabling support blockers or painting on supports manually. It takes a few minutes longer up front, but the material and time savings are absolutely worth it. Over time, this one setting has probably saved me more filament than any other.
3
Disabling unnecessary brim and raft settings
Only use them when you need adhesion help
Brims and rafts can help prints stick to the bed, but I used to leave them enabled out of habit, especially on tricky models. It turns out that’s a fast way to burn through filament for no real gain. I now only use brims for small parts or anything with a minimal first-layer footprint. For everything else, a simple skirt is enough to prime the nozzle and start the print cleanly.
When I need a brim, I reduce the default width from 8mm to 2 or 3mm. That still gives me adhesion without wasting as much filament or adding to cleanup time. Rafts, on the other hand, are now a last resort. They use a ton of material and often leave rough undersides. If I’m struggling with bed adhesion, I’m more likely to fix the bed surface, clean it, or tweak first-layer settings than rely on a raft.
This change made my first layers cleaner and more efficient. It’s also one less thing to remove after the print finishes. Once I realized how much plastic was going into these adhesion aids, I started using them more intentionally, making a noticeable difference.
2
Turning off prime towers by default
They’re helpful for multi-material but rarely needed otherwise
Prime towers serve a clear purpose in multi-material or multi-color prints, helping purge the nozzle clean between changes. But in single-material prints, they’re often unnecessary unless you’re printing something tall and thin or dealing with extrusion issues. I used to leave them enabled “just in case,” but now I disable them unless a specific print needs it.
This helps conserve not just filament, but also bed space and time. Prime towers add layers and transitions that the printer has to execute, which all add up, especially on long jobs. You probably don’t need one if you’re using a single nozzle and well-tuned retraction settings. Most artifacts they’re meant to prevent can be avoided with better temperature or movement tuning.
For multi-material prints, I still use them, just with the minimum size necessary to be functional. In all other cases, it’s off by default. That small toggle has saved me hundreds of grams of filament over the last few months alone.
1
Selective ironing for visual surfaces only
Save plastic and print time by targeting detailed areas
Ironing improves the top surface quality of your print by smoothing it out with a slow, extra pass. It’s a beautiful touch for lids, logos, and anything meant to be seen up close. But enabling it globally across every top layer is overkill, and wastes a surprising amount of time and filament. I switched to enabling ironing only on the top-most surfaces that matter visually.
This targeted approach is easy to set up in slicers like PrusaSlicer, where you can only limit ironing to flat top surfaces. The difference in quality is still noticeable where it counts, but you’re not dragging the nozzle across every square inch of the model. Ironing slows the print significantly and can introduce blobs or stringing if your extrusion isn’t dialed in. Keeping it selective avoids those headaches.
I use it mainly for aesthetic or functional parts with exposed surfaces. The rest get left alone. It’s another example of how one checkbox can add hours and dozens of grams to a print if you’re not paying attention.
Smarter slicing is the best way to reduce filament waste
After going through each of these settings, I saw a clear drop in how much filament I was using for the same number of prints. Some changes gave instant wins, while others took a little testing to get just right. But none of them sacrificed quality, and many actually improved it. That’s the sweet spot when it comes to slicer optimization.
It’s easy to let slicer defaults run the show, but those presets are designed to be safe and universal, not efficient. Tuning your settings to fit your printer and use case is where the real savings happen. These seven tweaks have helped me waste less, spend less, and get more reliable results across the board.